Analysis and explanation of typical problems in Hebei Zhipao's production and processing technology
About craftsmanship
First of all, we all understand the concept of craftsmanship. Its content and scope are very wide, ranging from design, production, type testing, transportation, installation, maintenance and so on. Use economical, reasonable and advanced processing methods to maximize the realization of design ideas. The role of craftsmanship should be distinguished from different understandings of craftsmanship and technological process. The meaning of craftsmanship is the guidance of drawings, and the meaning of craftsmanship is that the means of processing are processes and steps. The process document uses a combination of concise and concise language, process card flow and process drawing. Craftsmanship plays a very important role in the product.
Production process flow
1. Cutting process
The blanking process is the first production and processing process after the drawing is issued by the technical department. The production materials including plates and profiles must be cut according to the drawings. The relevant dimensions of the parts on the drawings are ultimately what the designer wants to achieve However, due to the attribute problems of each processing type in the production process, it is inevitable that there will be dimensional deviations. In many cases, in order to avoid the impact on product performance caused by this problem, we need to group welding together after cutting The parts are reprocessed. In this case, it is inevitable that the actual part size does not meet the requirements of the drawing. For this reason, we must be familiar with the processing technology when issuing two-dimensional drawings, and estimate the possible need for reprocessing. And leave a reasonable margin. The specific explanation will be given with an example after the next process.
The preparation of the process card requires the designer to have an understanding of the workshop's production and processing equipment, so that a more reasonable process card can be compiled to guide the workshop personnel in production.
Special-shaped pipe cutting machine
Intersecting wire cutting machine
CNC flame plasma cutting machine
Semi-auto flame cutting machine
Hydraulic sheet metal bending machine
CNC shearing machine
Profile roll bending machine
Horizontal band sawing machine
100 ton open tilting press
2. Riveting process
Type of welding
welding materials | Welding wire material | applicable |
drug core wire | ER501T-1 | This material is often used when welding important welds in equipment |
Solid welding wire | ER50-6 | This kind of material is often used in general welding of equipment |
welding rod | J422/J426 |
|
argon arc welding wire | THT50-6 |
|
Welding design
1) Principles of welding structure design:
The weld connection should meet the requirements of Article 8.2 of the "Code for Design of Steel Structures" GB50017-2003. Choose the types of materials reasonably, try to use standard parts, general parts and profiles, and design the structure reasonably. Try to adopt a simple and bright structure structure, adopt the simplest and most reasonable joint form, and the fewer types, the better, reduce short and irregular welds and avoid difficult-to-process spatial curved structures. Arrange welding seams reasonably, such as symmetrically arrange welding seams, avoid cross and dense welding seams, continuous welding seams for important work, intermittent welding seams for secondary welding seams, which is conducive to welding construction and reduces welding workload, and is easy to control Welding stress and deformation.
2) Basic requirements for welding structure design
(1) When designing the welding structure, it should be noted that when designing the welding structure, a reasonable structure and welding process should be adopted as much as possible to ensure:
① In meeting the design function requirements, the welding workload can be reduced to a minimum;
②Welding parts can no longer need or only a small amount of mechanical processing;
③Welding distortion and welding stress can be minimized;
④It can create good working conditions for welding operators;
⑤The structure has low production cost and high production efficiency.
(2) Reasonability of manufacturing:
The welded parts should have a good positioning datum---ensure the operability of assembly.
①Convenient operation when welding is considered, and the layout of welds should be considered for special structures. The minimum spacing during welding operations should be ensured when designing the structure.
②The position of the welding seam should minimize the number of adjustments of the welding equipment and the number of reversals of the workpiece;
(3) Economic rationality:
Consider the most effective welding position, and achieve the maximum effect with the smallest amount of welding. According to the structural characteristics of the product, try to design for flat welding and horizontal welding, avoid vertical welding and overhead welding. Under normal circumstances, try not to arrange the welding seam on the processing surface.
(4) Use safety aspects:
①Avoid designing welds in places where stress is easy to concentrate, especially important parts or welded parts that are subjected to repeated loads. This should be paid more attention to. Reasonably arrange the mutual positions of the construction to ensure the strength of the welded parts.
②The root of the weld should be avoided under tensile stress.
③For weldments that directly transfer the load, it is better to use the whole inlay joint, and turn the working weld into a contact weld
④ Box-shaped welded structural parts should be designed as tailored welding of bent parts as far as possible. Reasonable use of profiles, reduce welding seams, replace channel steel with two angle steel welding, welding is more convenient
⑤ Avoid excessive concentration of welds to prevent cracks and reduce deformation. At the same time, sufficient distance should be maintained between welds. To avoid the convergence of multiple welds, use the form of B.
⑥ Where there is an acute angle at the welding end, the angle should be made as slow as possible; the acute angle of the thin plate must be removed, because the sharp corner is easy to melt.
⑦The welds should be staggered to avoid cross welds, especially for thick sections.
⑧ When the concentrated load is applied to the T-joint, the place where the concentrated load is applied must be sufficiently rigid. Convenient construction and consider improving the working conditions of workers. When designing the structure, it is necessary to consider many problems in future construction, such as accessibility issues, and ensuring the necessary operating space for various constructions.
3) Examples of weld optimization design
(1) Improvement of swing arm design for Challenger's Journey:
Before improvement: Due to material procurement and other reasons, the main body of the swing arm is spliced by 7 cylinders.
Disadvantages before the improvement: there are 6 circular welds as shown in the figure; higher requirements for welding quality; difficult to control the integrity; increase the inspection workload.
Improvement measures: through consultation with the steel pipe factory, custom-made lengthened steel pipes that meet the design requirements.
Advantages after improvement: The annular weld is eliminated, and the influence of welding processing on the integrity and the uncontrollable factors of the welding process are eliminated.
(2) The layout of welds should avoid single failure welds:
When arranging the welds of the welded structure, avoid setting the entire weld on the same cross-section. Generally, misaligned butt welds are used. As shown in the figure, the beam and rod structure with tension and bending as the main stress is used.
(3) Flange welding structure:
The flange is a rolled plate, which is not isotropic. The metal is layered. The structure in Figure 1 is not good. It has not avoided the taboo of ""spalling"", only the weld A small number of metal layers in the connection position participate in the force. The weld is in tension, and once cracks appear, it will expand quickly. In Figure 2, more metal layers are involved in the force to avoid the problem of spalling, and the weld is changed to a shear weld that is not easy to expand, avoiding the use of a single failure weld.
Groove form
Groove: According to the design or process requirements, the groove of a certain geometric shape that is processed and assembled in the part to be welded of the weldment is called the groove. The groove is mainly used to weld the workpiece to ensure the welding degree. Under normal circumstances, the surface is processed by the machining method. According to the actual situation, most of the workpiece slopes of our company are processed by the flame cutting machine. Machining is performed only when you speak.
3. Machining process
The processing equipment in the machining workshop is now relatively complete. The machining work of most of our products has now gradually shifted from outsourcing to processing and production by itself (except for extra-large parts). ;Except for the planer, it is basically complete.
Horizontal milling and boring machine
CNC lathe
Heavy sleeper
Drilling machine
CNC wire cutting machine tool
Grinding machine
Hydraulic punching machine
Horizontal band sawing machine
4. Painting process
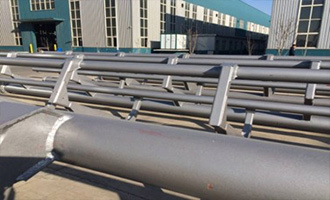
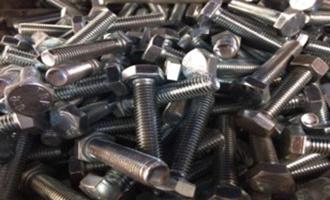
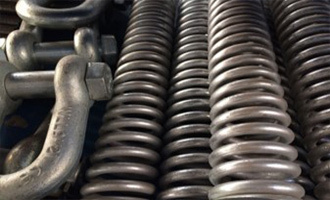
5. Assembly process
In the overall equipment, all the work involving the assembly of multiple pieces into another part is carried out in this section. For example, roller coasters---trains, high-altitude flying---seats, Ferris wheels---car brackets, interstellar flying saucers---pods, and so on.
There are certain deviations between product design drawings and physical production. A component may accumulate the deviations generated by the production and processing of multiple components during the assembly process. This requires us to consider it in the design process, so as not to affect In the case of product performance, try to avoid the value of cumulative deviation, or consider the appropriate assembly process during the assembly process. R&D is a method we often use in response to the above situations. In the actual assembly process, the assembly of the overall component can be better completed without affecting its performance.
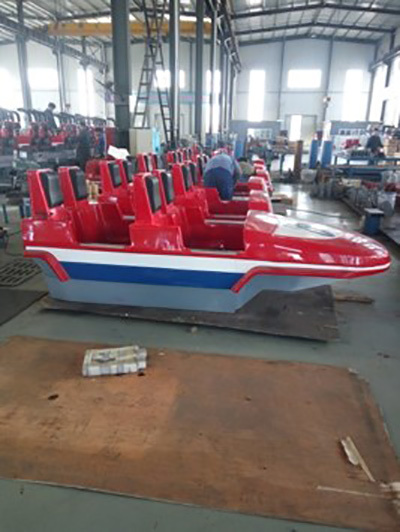
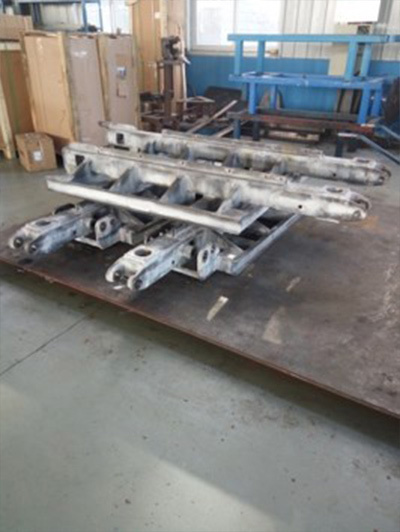
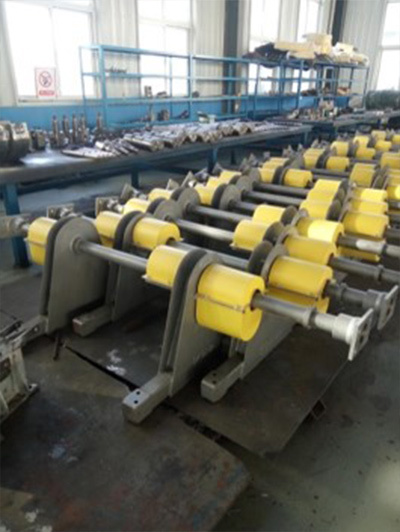
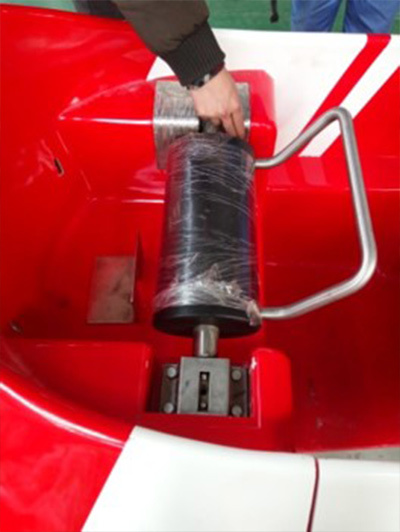
Comprehensive problems
1. Spherical roller bearing fits with the central shaft
The process error generated in the process of the taper of the shaft head will inevitably lead to the dimensional error in the horizontal direction when it is installed and matched with the spherical roller. This requires the adjustment of the left and right horizontal directions during the overall assembly, so reasonable assembly The process requires that one side is installed and fitted in place, and the other side has an adjustable space when installing the bearing. (The cooperation here requires the designer to have a deeper understanding of the machining and assembly process)
2. High-altitude flying 4 reducer adjusted to 2 reducer drive slewing ring
Reason for adjustment: The overall operation of the equipment is noisy. The main reason for investigation is poor synchronization in the process of driving the slewing ring by the reducer. In order to reduce the impact of this aspect, replace it under the condition that the driving power remains unchanged. The number of reducers with higher power is adjusted from 4 to 2 at first, and then the precision of the tooth surface processing of the pinion is improved to ensure better meshing performance between the pinion and the slewing ring.
3. Ferris wheel skateboard:
Initially, castings were used for processing and molding, because the defects in the casting process inevitably caused blisters or pores in the castings. Moreover, due to environmental management, most casting manufacturers have stopped production and the construction period cannot be guaranteed. Therefore, this method is no longer used for processing. Nowadays, the following two methods are often used to make this piece, one is to use δ 55 plate machine to form, and the other is to weld and form in three parts.
The two schemes have their own advantages and disadvantages, and different schemes can be selected according to the actual situation. In general, it is more economical and simple to use thick plates for processing.
4. Stress concentration treatment
1) Four and six ring roller coaster wheels:
The first-level weld requires full penetration welding, using argon arc welding for bottoming, and second-level welding cover. In order to reduce welding stress, annealing is performed after welding, and a process hole should be opened before annealing the closed cavity.
2) Fourth and sixth ring bridge housing:
In order to reduce the welding stress, perform annealing treatment after welding, and process holes should be opened before annealing the closed cavity.
5. Processing of certain holes in the assembly process
Welding process causes inevitably changes in the shape and size of the weldment, especially when it involves the assembly of two or more components, connect them with fasteners, and process the holes on the two pieces in advance. It is not a good choice, and it will cause difficulties in installing fasteners. In order to avoid this situation, hole matching is usually adopted, which can effectively avoid the above problems.
In addition, when a certain amount of clearance or a certain distance needs to be ensured during the installation of certain parts, the holes on the smaller parts are generally processed into long round holes to facilitate the realization of the design intent. Such as high-altitude flying, the processing of the hole position of the roller seat of the interstellar flying saucer revolution system.
6. Butt welding of pipes
Many of our company's products involve butt welding of pipes, such as roller coaster rails, Ferris wheel columns, etc. When the entire length of the purchased raw materials does not meet the use, it is necessary to weld multiple to achieve the purpose of use. To make the welding seam meet the strength requirements without losing its beauty, usually a round tube with a smaller diameter or a coiled plate is lined at the butt joint of the two pipes to achieve the purpose of welding. Otherwise, direct welding will form a clamp at the welding seam. The slag is not easy to clean and easily affects the quality of the weld, and finally the product fails to meet the requirements of use and is scrapped.
7. End flange connection pipe type
Most of the amusement equipment is exposed to the wild environment, and it is extremely necessary to prevent rain and rust. For example, pipes whose ends are connected by flanges. To avoid rain corrosion, except for the paint layer, a certain distance inside the port A round plate (square plate) should be welded to prevent the inflow of rainwater from causing internal corrosion.